International Online Workshop on Continuous Particle Synthesis and Product Design
From 4-6 October 2021, the Erlangen-based Collaborative Research Centre 1411 organised an international online workshop on continuous particle synthesis and product design. Continuous particle synthesis is of key importance for the understanding and scalable fabrication of complex particulate products. The generation of products with tailored properties, ideally multifunctional, is of utmost importance, requiring control of all five dimensions of size, shape, surface, structure and composition. To achieve this, a multidisciplinary approach is necessary, combining new reactors and reaction concepts for continuous manufacturing of new materials and products with modelling, simulation and optimization. Materials of interest range from noble metals and semiconductors, porous materials like metal organic frameworks to polymers and pharmaceutical materials. These can be agglomerated into so-called supraparticles that form superstructures with tailored and completely new – for instance optical – properties. Characterization, ideally inline, and process control are additional pillars, which are mandatory to achieve new materials with new properties with high throughout and on demand.
Experts with the diverse perspectives described above reviewed the status quo of the continuous synthesis of particulate products using state-of-the-art and newly developed methodologies.
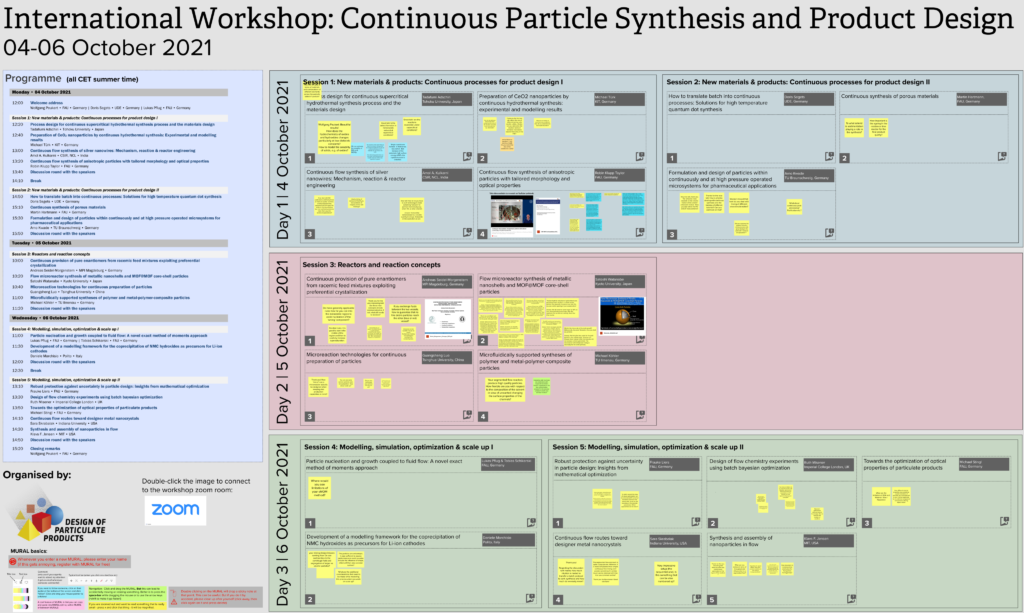
A special focus was laid upon the identification of key challenges and intersections of the different techniques. The latter is of particular importance, as the fabrication of complex particle systems of continuously increasing complexity require diverse and interdisciplinary approaches and multidisciplinary teams. The scientific exchange between different experts in the field of particle synthesis and product design aims to identify future prospects of continuous particle formation. Overall, the workshop promoted intense discussions and exchange between the participants.
Programme, Speakers and Abstracts
All times Central European Summer Time (EDT + 6, BST + 1, AEST – 8).
12:00 |
|
|||
Session 1: New materials & products: Continuous processes for product design I |
||||
12:20 |
In this lecture, first the specific features of continuous “supercritical hydrothermal synthesis” process will be explained. Metal salt aqueous solution is fed to the tube reactor and mixed with high temperature supercritical water fed from another line, and thus hydrothermal reaction occurs. At the exit of the reactor, the product was cool down by a cooling water jacket. Pressure of the system was controlled by a back-pressure regulator. Thus, in this system, the reaction temperature/pressure and the residence time of reactant solution can be precisely controlled. Effect of the mixing in the reactor, namely Re number, on the reaction kinetics and particle size/distribution was evaluated. The results clearly indicated the rational design of small particle size and narrower size distribution, based on the fluid dynamics and kinetic. Under this condition, hydrogen gas can form homogeneous phase with supercritical water, and thus the reducing atmosphere can be controlled. This lead to the formation of metallic nanopartciels. In the supercritical state, organic molecules is miscible with water, which lead to synthesize organic modified nanoparticles. Kinetic study of nucleation and organic modification have been done for designing the continuous SHS reactors. Organic modified nanoparticles can broaden the application of NPs, such as highly concentrated nano inks for inkjet 3D printing, fabrication of transparent high reflective index film (ARF), high heat transfer hybrid film etc. Designing those nano hybrid materials based on the thermodynamic approach, phase behavior and property estimation, will be introduced at the end of this lecture. |
|||
12:40 |
The development of novel chemical processes that allow controlling the particle size, size distribution and morphology of catalytic active nanostructures enables new possibilities for energy-related applications and automotive emission control. Among others, Ceria (CeO2) is one of the most promising materials for environmental and energy related applications. For example, CeO2 can be used as the active component of the catalyst or as the substrate of noble metal catalysts for the CO and propane oxidation [1]. Furthermore, reducing the CeO2 particle size to the nanoscale has a significant influence on the catalytic behavior [2,3]. A promising method to synthesize nano sized particles with well-defined properties is the Continuous Hydro-Thermal Synthesis (CHTS) that is based on the mixing of a cold aqueous metal salt solution with hot compressed water [4,5]. However, a deeper understanding of the relationship between synthesis conditions (e.g. temperature, pressure, mass flow rate and type of salt) and the obtained product properties (i.e. catalytic activity and selectivity) is currently not yet available.
References: |
|||
13:00 |
Continuous flow synthesis of nanomaterials helps to achieve consistency in the material properties viz. dimensions (size or size distribution and shape), optical properties, electric properties, etc. The laboratory scale flow synthesis of nanomaterials has been demonstrated successfully for several materials. Taking laboratory scale synthesis to large scale manufacturing is a rather more challenging task when compared to scale-up for conventional organic or inorganic compounds where purity is more important and the physical forms do not matter at the reactor outlet. However, for the case of nanomaterials, the situation becomes more challenging as the energy supplied at a relatively much larger scale needs to deliver effects at nanometer length scales. Considering this aspect, it is necessary to control the reaction rates at a sub-microscopic length scales and ensure that the macroscopic effects are well understood so as to control the energy supply. In this presentation, we will present a detailed analysis of the nature of mixing and heat transfer at macroscopic condition on the synthesis of silver nanowires (Sun et al. 2002) in a cascade of continuous flow reactors (Kulkarni et al. 2019). The nature of flow patterns are also seen to control the encapsulation/coating of PVP on the nanowires thereby needing additional washing steps to make them useful for conducting inks. The nanowires synthesized from various approaches were subsequently used for making different formulations of conducting inks. ![]() References |
|||
13:20 |
Currently there is an increasing trend to produce functional nanoparticles using continuous flow liquid phase synthesis. This approach enables more precise control over mixing processes which may strongly influence nucleation and growth events and affect the distribution of nanoparticle morphologies and properties. Moreover, for complex particulate products, typically produced in multi-step, small volume batch syntheses, continuous flow methods offer a realistic opportunity for up-scaling while maintaining the target property, which is often strongly dependent on particle size and shape. In this contribution I will describe my group’s work to produce so-called patchy particles using simple T-mixers and with attainable production rates up to several grams per hour. Our material system comprises nanoscale gold or silver patches on polystyrene or silica core particles. This arrangement provides both a tunable anisotropic morphology and application-relevant optical properties resulting from the localized plasmon resonances of the patches. After showing how our small-volume batch syntheses could be realised as continuous flow processes I will illustrate how we used these to support investigations of the patch formation mechanism. With deeper understanding of the latter, we have recently recognised the advantage of moving from single step patch formation processes to two step ones. I will show how this can be realised without significant increase in process complexity by employing T-mixer cascades. |
|||
13:40 | Discussion with the speakers | |||
14:10 | Break (40 Minutes) | |||
Session 2: New materials & products: Continuous processes for product design II |
||||
14:50 |
Quantum confined semiconductor nanoparticles (NPs) known as quantum dots (QDs) are attracting a lot of attention due to their tailored optical absorption and emission that strongly depend on particle size, composition and surface. QDs are promising materials for displays, solar cells, memory chips, sensors and theranostics, however, their design and scalable production remains a challenge. In this contribution, I will first demonstrate by means of the continuous synthesis of ZnO quantum dots, how particle technology can team up with mathematical optimization to adjust products with tailored optical properties. In the second part of my talk, I will introduce concepts for replacing the tedious batch synthesis of QDs by hot injection using a customized continuous reaction setup. |
|||
15:10 |
Abstract will follow soon. |
|||
15:30 |
Abstract will follow soon. |
|||
16:10 | Discussion with the speakers |
All times Central European Summertime (EDT + 6, BST + 1, AEST – 8).
Session 3: Reactors and reaction concepts |
|
10:00 |
Crystallization is one of the most effective ways to separate mixtures of enantiomers. Kinetically controlled Preferential Crystallization (PC) has proven to be applicable to provide pure enantiomers from racemic mixtures of conglomerate forming systems [1, 2]. Nowadays, primarily periodically carried out seeded batch processes are applied. References |
10:20 |
Core-shell type particles are attractive because they can impart novel functional properties due to synergistic effects between core and shell materials. Controlling core size and shell thickness is a key for exploiting full potential of these particles for desired applications, although it has been challenging. The widely used batch-type reactor synthesis generally suffers from producing uniform core-shell structures because of poor reactant mixing especially when the reaction rate is faster than that of mixing. A microreactor is a promising alternative for the core-shell particle synthesis because it ensures excellent mixing, thereby enabling to control core size and shell thickness. In this study, we applied a microreactor to the synthesis and successfully synthesized SiO2@Au,[1] SiO2@Ag,[2] and metal-organic framework (MOF)@MOF core-shell particles.[3] Our approach was the direct deposition of shell materials through heterogeneous nucleation on the core particle surface by mixing a core particle suspension with a reaction solution of a shell material. A key requirement for the successful shell formation was to quickly bring a reaction mixture into a uniform dispersion of core particles in a uniform reaction solution, and the excellent mixing ability of the microreactor facilitated the realization of the uniform reaction field so that the heterogeneous nucleation was preferentially induced. The quick and homogeneous mixing provided by the microreactor was found to be critical in the formation of uniform core-shell particles, as opposed to a batch reaction process. In this way, we have successfully established the flow synthesis of uniform core-shell particles by taking advantage of the excellent mixing performance of the microreactor. [1] S. Watanabe, T. Hiratsuka, Y. Asahi, K. Mae, and M.T. Miyahara, Part. Part. Syst. Charact. 32, 234 (2015). |
10:40 |
Microflow chemical processes have high promising prospects for the low-carbon and sustainable development. They are also expected to make some great changes in the continuous preparation of particles. As to the continuous preparation of nano/micro particles in microreaction systems, it is well understood that microchemical systems could provide a powerful platform for preparation, functionalization, and manipulation of nano/micromaterials. The research group of microreaction engineering at Tsinghua University has carried on the nano/micro particle preparation with microchemical systems for long time. Our work covers the synthesis strategies based on novel microfluidic devices and microreaction systems, and the preparation of novel functional nano/micromaterials. Some industrial applications of microreaction systems in the continuous preparation of particles have been successfully realized. |
11:00 |
Polymer micro and nanoparticles and metal-polymer composite particles are of interest for process engineering as well as for new applications in miniaturized chemical analyses, in solid-state synthesis and heterogeneous catalysis. Such particles can advantageously be prepared by microfluidic process steps. In particular, droplet-based microfluidics supports the formation of particle populations with high homogeneity in size, shape and composition. Well-controlled flow rates, flow rate ratios and local streaming conditions are important for achieving a high reproducibility in droplet generation, in particle formation and in further modification steps. Polymer nanoparticles of different size which are formed in an emulsion polymerization, can be produced by use of a micro hole plate reactor. The particle size can be tuned by surfactant concentration and flow rates. Noble metal nanoparticles from micro segmented flow syntheses can be immobilized on the surface of these polymer particles. In result sub-micron particles carrying Au-, Ag-, Pt-, Rh- and Pd- components have been obtained. The typical sizes of the metal nanoparticles are in the range between some and some tens of nanometers, the sizes of the composite particles between about 0.2 and 0.8 µm. The manageability of composed submicron particles can be improved by depositing them as a film on hydrogel particles with diameters in the middle or upper micron level or by incorporating them inside the matrix of such swellable larger particles. These hydrogel particles can be prepared microfluidically by a continuous droplet formation and following photopolymerization process. One of these hydrogel particles can carry millions of the active small metal-polymer composite particles. Silver nanoparticle-containing polymer and hydrogel particles are well suited for surface enhanced Raman spectroscopy (SERS). Analytical tests showed that concentrations down to the nanomolar range can be detected in sampling volumes of one or a few microliters by use of single of these metal-containing sensor particles. The catalytic activity of metal-polymer composite particles was checked by experiments of chemical dye bleaching. In these experiments, a small set of the catalyst particles was fixed inside a capillary and a reaction mixture was conducted over them. The rate of bleaching reaction was determined by measuring the optical density before and after the catalyst particles using micro flow-through photometers. In the size range between a few nanometers and one millimeter, a huge number of differently constructed complex particles could be formed. Microfluidic techniques offer important advantages for investigating the processes of particle formation, for synthesis of hierarchically constructed particle architectures and for the development of new particle-based functional materials. |
11:20 | Discussion with the speakers |
All times Central European Summertime (EDT + 6, BST + 1, AEST – 8).
Session 4: Modelling, simulation, optimization & scale up I |
|
11:00 |
The local supersaturation build-up governs the nucleation and growth of (nano-) particles, whereas the mixing of the two reacting chemical compounds determines the supersaturation. The classical approach to mathematically model such precipitation processes relies on the population balance equation for the disperse phase coupled with the Navier-Stokes equations for the fluid flow. However, even for the simplest mixing case, namely two initially segregated chemical compounds exposed to a laminar (parabolic) flow profile, solving the governing equations is numerically challenging, in particular, when the particle size distribution is of interest. This is due to the strong nonlinear coupling between the involved subprocess and their acting on different time and length scales. This is why we will introduce in this talk, a novel numerical approach, which in future can serve as the gold standard in terms of accuracy. In the first part of the talk, we will introduce the theoretical background consisting of a reformulation of the nonlinear (and nonlocal in terms of the disperse coordinate) governing equations only in terms of solely the educt concentrations in space and time. The resulting equations can be efficiently solved as a fixed-point problem and allow an exact reconstruction of the entire particle size distribution. In the second part of the talk, we will demonstrate the reformulation’s practical implementation. The focus here is on a comparison of the novel numerical approach to common existing methods such as classical moment methods. In particular, we will show when the well-known classical moment methods succeed and fail in approximating the solution of the governing equations accurately. Finally, we will discuss how the reformulation can be used to exactly reconstruction the particle size distribution from the moments obtained by classical moment methods. |
11:30 |
In this talk we will discuss the modelling and simulation framework, based on computational fluid dynamics (CFD) and population balance equation (PBE), for the simulation of nickel-manganese-cobalt hydroxides coprecipitation from solution, developed during the EU project Simdome (https://simdome.eu/). Nickel-manganese-cobalt (NMC) hydroxides and precursors for NMC cathodes, widely used in Li-ion batteries. The coprecipitation is a standard reactive crystallization process, where metal sulphates are mixed with ammonia and sodium hydroxide to induce the formation of particles via the classical mechanisms of nucleation, molecular growth, aggregation and breakage. The model accounts for mixing and fluid dynamics, via CFD and compartment models derived from CFD, micro-mixing, via a multi-environment model, and particle formation and evolution, via a PBE solved with the quadrature method of moments (QMOM). All the chemical equilibria in solutions, as well as non-idealities, are accounted for. The missing kinetics parameters appearing in the nucleation, molecular growth and aggregation models are identified via an optimization algorithm. Model predictions are in line with experimental observations and elucidate the role of the different phenomena involved. |
12:00 | Discussion with the speakers |
12:30 | Break |
Session 5: Modelling, simulation, optimization & scale up II |
|
13:10 |
Deciding on a high-quality experimental setup for particle design is challenging. In addition, protection against uncertainties is needed. In this talk, we review mathematical methodologies for robust hedging against uncertainties. We will give insights into such robust approaches for both particle synthesis together with an outlook to particle chromatography. |
13:30 |
Advances in chemical engineering laboratory technologies are transforming traditional “trial-and-error” experimental paradigms [1,2]. Specifically, experiments can be miniaturized and run extremely quickly in the form of microreactors/microdroplets. New measurement techniques further expedite laboratory processes by enabling rapid analyses of experimental outcomes. Given the above, experiments can be performed in high-throughput and must be designed quickly; at times samples must be taken even before receiving full results from previous experiments (e.g., due to measurement time delay). To this end, recent works, such as [3-5], have focused on “self-optimizing,” or “closed-loop” experimental platforms, which update the design of future experiments continuously as experiments are performed. In most cases, these self-optimizing platforms seek solely to optimize a given performance criterion, rather than to develop a predictive mathematical model as in traditional model-based design of experiments. Therefore, a common strategy is to combine mathematical optimization with a Gaussian Process surrogate model that predicts the outcomes of future experiments in a Bayesian Optimization framework. This work investigates how high-throughput flow-chemistry experiments can be continuously and systematically designed, while accounting for (uncertain) varying experimental timeframes and heterogenous measurements. We propose a new approach that leverages developments in multi-fidelity [6] and batch [7] Bayesian Optimization. These techniques provide, respectively, statistical frameworks for optimizing experimental regimes with different available measurements and with multiple experiments (i.e., an “asynchronous batch”) occurring simultaneously due to associated time delay(s). Our computational studies on black-box optimization of both industrially relevant and standard test instances show that the proposed methods perform favorably compared to random sampling and traditional Bayesian Optimization approaches. [1] Houben, C., & Lapkin, A. A. (2015). Automatic discovery and optimization of chemical processes. Current Opinion in Chemical Engineering, 9, 1-7. |
13:50 |
Challenges in designing optical properties of particulate systems by topology and shape optimization approaches will be discussed: first, already on the individual particle level, the question for an optimal topology, shape and composition leads to a high resolution of the design space. Second, optical properties often depend on the full spectrum of visible light and thus time-harmonic Maxwell’s equation has to be solved for many wave-lengths. Third, often results are expected to be angle-independent, which implies that arbitrary particle orientations have to be taken into account. And fourth, in real-world systems, distributed properties (for size, shape, composition …) have to be taken into account. All this leads to an optimization problem, in which a single evaluation of the objective requires thousands of state problems to be solved. In this presentation, we show how these difficulties can be approached. Furthermore relations to particle synthesis are discussed. |
14:10 |
Mono- and multimetallic nanocrystals have diverse and tunable physicochemical properties that arise from their compositions as well as crystallite size and shape. The ability to control precisely the composition and structure of nanocrystals through synthesis is central to achieving state-of-the-arrt designer metal nanocrystals for use as catalysts and electrocatalysts. However, a major limitation to the use of designer metal nanocrystals is the ability to scale their syntheses while maintaining structural precision. To address this challenge, continuous flow routes for the synthesis of metal nanoparticles involving the use of droplet microreactors are being developed and will be discussed in this presentation. As will be shown, these droplet microreactors provide the synthetic versatility necessary to achieve known and completely new nanostructures, with integration of computational tools and inline spectroscopies offering exciting opportunities for adaptive flow routes for designer metal nanocrystals. |
14:30 |
Continuous flow systems are shown to have advantages in synthesis and assembly of nanomaterials, including faceted metal nanoparticles, quantum dots, and nanodendrites. Synthesis in flow leads to sharper size distribution and more reproducible growth than typically achieved in batch processes. The choice of reactor configuration, solvents, reagents, and exposure environment has significant impact on the resulting nanostructures. Using multiple flow systems in series provides control of nucleation, growth, ageing, and over-coating of core-shell nanoparticles, as exemplified with the synthesis of InP quantum dots. Sequential flow synthesis steps also enable synthesis of hierarchically structured nano and meso scale structures. |
14:50 | Discussion with the speakers |
15:20 | Closing remarks by Wolfgang Peukert (FAU, Germany) |